Schaltungen mit LED-Effekten wirken immer wieder sehr faszinierend. Eine der beeindrucktesten Schaltungen der letzten Jahre ist die sogenannte „Propellerclock“ bzw. das „Propellerdisplay“. Im wesentlich handelt es sich hier um eine Platine mit einer Reihe von Leds die in hoher Geschwindigkeit gedreht wird. Durch genaues Timing werden dann die Leds so zum Leuchten gebracht, das es für das Auge so erscheint als würde ein leuchtender Schriftzug oder auch eine Grafik mitten in der Luft geschrieben. Zustande kommt dies durch die Trägheit des Auges.
Oft werden die Leds auch so zum Leuchten gebracht das eine analoge Uhr frei schwebend in der Luft erscheint, daher der Name Propellerclock.
Zahlreiche Bastler haben schon Propelleruhren in den unterschiedlichsten Varianten gebastelt, die Idee ist also nicht neu. Da auch mich die Anzeige immer schon fasziniert hat und das ganze ein tolles Design-Objekt darstellt, bin ich dieses Projekt auch mal angegangen. Und damit auch andere Bastler was von haben, gebe ich meine Erfahrungen gerne in dieser Projektbeschreibung weiter.
Welche Probleme müssen gelöst werden?
Leider ist der Aufbau und die Programmierung einer solchen Propellerclock nicht ganze einfach, ein wenig Erfahrung in Sachen Elektronik sollte vorhanden sein. Damit die Propelleruhr wirkt darf sie nicht zu klein sein.
Alleine das ist schon ein Problem denn viele Bastler haben bestenfalls ein Freeware CAD-Programm wie Eagle. Mit der Freeware Version sind jedoch nur sehr kleine Platinen möglich, für eine Propellerclock reicht das nicht aus.
Ein weiteres Problem ist die Bauteil Auswahl. Die Bauteile müssen klein sein und so verteilt werden das möglichst wenig Unwucht entsteht. Bei hohen Drehzahlen bedeutet eine größere Unwucht erhebliche Vibrationen und einfach richtig Krach. Das stört nicht nur den Effekt sondern zerstört nach kurzer Zeit auch die Motorlager. Wenn ihr Pech habt dann fliegt euch auch noch die Platine um die Ohren.
Und noch ein weiteres größeres Problem ist die Stromversorgung der drehbar gelagerten Platine. Wie soll man die Platine mit Strom versorgen wenn sie sich schnell drehen soll, Kabel sind somit nicht möglich. Man muss also zu Schleifern oder induktiver Übertragung übergehen.
Und zu guter letzt dann noch die Programmierung! Wie bekommt man das Timing hin?
Sehr lehrreiches Projekt
All diese und noch weitere kleine Probleme müssen gelöst werden damit am Ende ein beeindruckendes optisches Ergebnis steht. Gerade das macht diese Schaltung aber auch sehr reizvoll und lehrreich. Es gibt nur wenige Schaltungen die so viel Spaß und dennoch so viele verschiedene Grundlagen vermitteln.
Diese Dokumentation soll eine Möglichkeit aufzeigen wie man eine solche Propelleruhr realisieren kann.
Zur Unterstützung könnt ihr einen fertigen Entwurf der beschriebenen Platine als Eagle-Datei herunterladen und bei bedarf bei einem Platinen-Produzenten herstellen lassen. Natürlich könnt ihr die Eagle-Datei auch nur als Anregung nutzen und nach eigenen Vorstellungen verändern, allerdings ist hier eine Eagle-Version nötig welche die Platine in voller Größe darstellen kann, ich glaube die Freeware-Version reicht da nicht aus.
Trotz Platine handelt es sich dennoch nicht um ein leichtes Projekt, denn der mechanische Aufbau bleibt einem weitestgehend selbst überlassen, dieser Beitrag soll allerdings viele hilfreiche Tipps dazu geben.
Auch die vorgestellten Programme und Lösungen sind keineswegs das Endstadium meines Propellerclock Projektes sonder zeigen nur den ersten Schritt und helfen zum ersten Erfolg zu kommen . Die Schaltung erlaubt noch viele weitere Möglichkeiten wie induktive Datenübertragung. Was letztlich draus entsteht und welche Möglichkeiten der Platine ihr nutzt bleibt jedem selbst überlassen, wie gesagt dieser Beitrag soll nur etwas helfen und praktische Erfahrungen zu vermitteln.
Wichtig – Sicherheit beim Basteln
Wichtig ist das eine absolut feste Verbindung zwischen Platine und Motorwelle entsteht. Diese muss auch den Belastungen einer höheren Drehzahl (min. 1500 UMin) aushalten. Geht hier also auf Nummer sicher denn eine umherfliegende Platine kann erhebliche Verletzungen verursachen.
Es wird auch dringend empfohlen eine Art transparente Haube zu basteln, die über die drehende Platine gestülpt wird. Nur so ist sichergestellt das ihr euch nicht bei der drehenden Platine verletzen könnt.
Welcher Motor / Welche Bildwiederholfrequenz
Im Grunde eignet sich fast jeder Gleichstrommotor zum drehen der Platine. Es werden keine sehr großen Anforderungen an den Motor gestellt, jedoch sollte diese bei der verwendeten Spannung eine Umdrehungszahl zwischen 800 und 1500 Umdrehungen pro Minute nicht überschreiten. Das bedeutet also das unsere Propelleruhr später eine Bildwiederholungsrate von ca. 15 bis 25 Bilder pro Sekunde hin bekommen würde. Das Reicht für hochauflösende Darstellungen und Effekte aus. Viel höhere Bildwiederholungsraten sind mit der Schaltung nicht drin, da die LED-Treiber maximal mit 1Mhz Bus per I2C angesteuert werden müssen.
Sollte der Motor eine höhere Nenndrehzahl haben, so kann man diese gewöhnlich durch reduzieren der Spannung reduzieren. Natürlich könnte man die Geschwindigkeit des Motors auch per PWM mit einem weiteren Controllerboard (z.B. RN-Control) steuern, aber gewöhnlich ist das nicht notwendig.
Ideal eignen sich auch viele PC-Lüfter. Einige Restposten-Anbieter bieten sehr günstig Lüfter mit niedrigen Drehzahlen an. Diese eignen sich sehr gut da sie meist sehr laufruhig sind und eine sehr konstante Drehzahl bieten. Bei meinem Test habe ich einen solchen Lüfter mit 1500 U/Min genutzt. Die Flügelblätter wurden einfach mit einen kleinen Minibohrmaschine mittels Trennscheibe herausgeschnitten. Der Rest wurde mit einem Minifräser sauber weggeschliffen. Dadurch entfällt dann auch das restliche Luftgeräusch und der Lüfter ist kaum noch zu hören. Mit Platine hat unser Lüfter dann bei 12V ca. 1000 und bei 16V ca. 1236 UMin geleistet, also max. 20 Bilder pro Sekunde. Die Fotos in diesem Beitrag wurden mit 17 Bilder pro Sekunde geschossen, genau wie das Video. Wenn man nur 16 statt 32 Leds nutzt, kann man die Bildwiederholfrequenz auch noch erheblich erhöhen.
Um die genaue Drehzahl eures Propellers zu ermitteln habe ich noch ein Programm “umdrehungenzaehlen.bas“ am Ende des Beitrags zum Download bereitgestellt. Einfach in den Hauptcontroller der Propelleruhr laden und dann dieses starten. Das Programm wartet bis der Motor voll läuft und zählt dann die Umdrehungen. Nach einigen Sekunden wird das Ergebnis endlos über die RS232 ausgegeben. Aber steht alles in den Kommentarzeilen zum Programm.
Die Stromversorgung
Wie schon erwähnt stellt die Stromversorgung der Platine eine besondere Herausforderung dar. Unsere Platine kann bis zu 50 Leds aufnehmen und ansteuern. Die Stromaufnahme kann also Spitzenwerte von ca. 1 A erreichen. Ein Betrieb per Akku macht daher wenig Sinn.
Es bleiben also nur zwei Möglichkeiten:
- Man befestigt an der Motorachse zwei Ringe an die man einen Draht anlötet und mit der Platine verbindet. Zwei Schleifer müssten dann während sich die Achse mit den Ringen dreht die Spannung durch Berührung übertragen.
Nachteil: Nicht ganz einfach umzusetzen und ein gewisser mechanischer Verschleiß der Schleifer wenn man es nicht richtig auslegt.
Vorteil: Auch höhere Ströme lassen sich relativ gut übertragen - Eine zweite Möglichkeit ist die induktive Übertragung von Spannung. Man kennt das Prinzip vielleicht von der elektrischen Zahnbürste. Diese wird aufgeladen ohne dass sie eine elektrische Verbindung zum Ladegerät besitzt.
Nachteil: Wirkungsgrad ist oft nicht toll und Aufbau ebenfalls nicht sonderlich leicht. Durch die Spulen wird die Propellerclock gewöhnlich etwas tiefer und Unwucht Probleme kommen schnell auf.
Vorteil: kein Verschleiß
Ich habe mich bei diesem Projekt für Methode 2 (induktive Stromübertragung) entschieden, was nicht heißt das Methode 1 nicht auch sinnvoll ist.
Die Platine ist so ausgelegt das beide Methoden möglich sind. Sie muss einfach nur mit einer Spannung zwischen 7 und 18 Volt versorgt werden. Dabei ist es ihr sogar egal ob es Gleichstrom oder Wechselstrom ist. Auch wie der Gleichstrom an dem vorgesehenen Anschluss (POWER) gepolt wird, ist der Schaltung egal (dank Brückengleichrichterschaltung).
Induktive Stromübertragung
Um die Schaltung möglichst einfach mit der notwendigen Spannung zu versorgen brauchen wir zwei Spulen die ineinander stecken. Eine der Spulen muss sich mit der Platine drehen und eine andere muss fest stehen und mit einer Wechselspannung versorgt werden. Die fest stehende Spule erzeugt dadurch ein Magnetfeld und induziert somit eine Spannung in der anderen Spule. Die Spannung und der Strom müssen dann nur noch ausreichen um die Platine zu versorgen. Ob die innere oder äußere Spule als Primär- oder Sekundär –Spule genutzt wird ist dabei völlig egal.
Das ganze hört sich einfach an, aber in der Praxis ist es gar nicht so einfach die richtigen Drahtdurchmesser, Windungszahl und Frequenz der Wechselspannung zu finden. Ich habe bestimmt über 10 Spulen gewickelt um an brauchbare Ergebnisse heranzukommen. Hier müsst ihr einfach ein wenig experimentieren, wobei nachfolgende Tipps euch schon sehr helfen müssten:
Die Spulen sollten einen nicht zu kleinen Durchmesser besitzen. Gute Werte habe ichr erst mit Spulen von mindestens 4cm Durchmesser erzielt. Ideal sind wohl für unser Projekt Spulendurchmesser zwischen 40 und 70 mm. In der Praxis eignen sich Kunstoff HT-Rohre (Abwasserrohre) aus dem Baumarkt sehr gut für solche Spulen. Auch die Stopfen solcher Rohre können gut verwendet werden, an sie kann man dann auch gut die Platine anschrauben.
Innere und äußere Spule sollten möglichst dicht aneinander sein. Je dichter sich die Windungen gegenüberstehen desto höher der Wirkungsgrad, also je besser die Stromübertragung. Allerdings muss man auch darauf achten das eine geringe Unwucht nicht dazu führt das sich innere und äußere Spule berühren, sie würden sich sehr schnell zerstören und zudem würde der Motor nicht mehr gleichmäßig drehen. Also keine Sorge wenn der Abstand etwas größer aus fällt, es klappt notfalls auch noch bei 3-5mm Abstand, allerdings halt mit schlechteren Wirkungsgrad.
Im Inneren der Spulen sollte möglichst wenig Metall vorhanden sein. Ist das Metall zu nah an den Wicklungen beeinflusst dies das Magnetfeld und den Wirkungsgrad sehr ungünstig. Also nicht auf den Gedanken kommen den Motor direkt zu umwickeln. Zumindest ein kleiner Abstand muss sein!
Die Wicklungszahl darf nicht zu groß gewählt werden. Oft denkt man je mehr desto besser, aber das ist leider falsch. Werden zu hohe Windungszahlen gewählt, so erhöht sich nicht nur die Induktivität der Primärspule sondert auch der induktive Widerstand. Ein hoher induktiver Widerstand gestattet dann keine größeren Ströme mehr. Gute Ergebnisse haben Wicklungszahlen von ca. 30 bis 40 Windungen bei der Primärspule ergeben. Bei der Sekundärspule sollten es einige Windungen mehr sein, hier haben 40-60 Windungen ein gutes Ergebnis gezeigt. Es kommt natürlich immer auch auf die Frequenz der Wechselspannung an, dazu gleich mehr. Bei der Primärspannung gehe ich bei den genannten Angaben mal von 10 bis 15 Volt aus.
Der Drahtdurchmesser der Spulen sollte nicht zu dünn werden. Unsere Schaltung kann bis zu 1A ziehen. Bedenkt man dann noch dass der Wirkungsgrad oft nicht toll ist, so kann primär durchaus 1,5 bis 2A gezogen werden, bei niedrigen Frequenzen sogar noch mehr. Die Spulen sollten sich bestenfalls nur gering bis gar nicht erwärmen. Brauchbare Ergebnisse zeigten Primär min. 1mm² Draht und Sekundär 0,8mm² Draht.
Eine übliche Wechselspannung von 50 Hz reicht leider nicht aus um genügend Strom auf die Sekundärspule zu übertragen. Es ist daher zu empfehlen eine Wechselspannung mit höherer Frequenz zu generieren. Je weniger Windungen die Primärspule besitzt, desto höher kann die Frequenz sein. Bei oben genannten Richtwerten haben sich Frequenzen zwischen 12khz und 20khz als optimal erwiesen. Darunter und darüber sinkt der Wirkungsgrad, was man leicht durch Messen der Spannung an der Sekundärspule (am besten bei Belastung) feststellen kann.
Beispielaufbau
Das Bild zeigt unseren Beispielaufbau. Auf die Nabe des Lüfters wurde die Sekundärspule (40mm Rohr) aufgebracht und daran die Platine angeschraubt. Außen herum wurde die Primärspule auf ein etwas größeres Rohr gewickelt. Dieses Rohr ist am Rahmen angeklebt. Im Bild sieht man also nur die Primärspule. Der Rahmen des Ventilators ist dann mit Gummiringen als Schwingungsdämpfung an einer Acrylglasplatte, die als Ständer dient, befestigt. Letzteres ist nicht unbedingt nötig da unser Lüfter ohnehin sehr ruhig läuft und kaum eine Unwucht aufzeigt. Man muss genau darauf achten das man die Rohre und Platine möglichst genau mittig platziert, sonst nerven die Vibrationen / die Unwucht schon erheblich. Das empfand ich auch als größte Schwierigkeit bei dem ganzen Projekt. Das Wickeln der Spule hingegen ist nicht sonderlich schwierig. Es ist nicht weiter schlimm wenn die Windungen mal nicht ganz genau nebeneinander liegen und die Windungszahl nicht 100% genau stimmt. Damit die Windungen bei wickeln nicht verrutschen kann übrigens etwas doppelseitiges Klebeband auf dem Rohr (Spulenkörper) sehr hilfreich sein.
Wechselspannung generieren
Kommen wir zurück zur Wechselspannung die für die primäre Spule nötig ist. Am einfachsten lässt sich diese ebenfalls über einen kleinen Microcontroller erzeugen. Das hat auch den Vorteil das man sehr leicht verschiedene Frequenzen programmieren und ausprobieren kann. Ein weiterer Vorteil besteht darin, das man über die Betriebsspannung auch Daten an die Propellerplatine übertragen könnte, aber dazu später.
Zur Erzeugung der Wechselspannung verwendet man am besten einfach einen kleinen Motortreiber. Dieser sollte allerdings mindestens 2A aushalten. Es ginge zum Beispiel mit dem IC L298, allerdings wird dieser schon mächtig warm bei dem benötigten Strom. Ideal ist dafür ein Motortreiber der Firma Pololu (36V9), welcher auch in einige deutschen Shops erhältlich ist. Er hat soviel Leistungsreserven das er sich quasi noch nicht mal erwärmt. Er hat noch einen anderen Vorteil, nämlich die Ansteuerung mittels DIR Eingang. Zur Erzeugung einer optimalen Wechselspannung legt man einfach den PWM-Eingang dauerhaft auf High und versorgt den DIR-Eingang mit einer Frequenz die man per Timer generiert. Das Software-Programm kann dann besonders einfach ausfallen. Verwendet man doch den L298 so müsste man in einer Interrupt Routine stets die Eingänge IN1 und IN2 umpolen was einen erheblich größeren Rechenaufwand bedeutet. Der Controller könnte dann bei hohen Frequenzen nicht mehr allzu viel anderes machen. Ginge aber auch!
Durch den Richtungswechsel ergibt sich am Ausgang eine optimale Rechteck-Wechselspannung die man direkt auf die Primärspule leiten kann. Im Test ergab das optimale Ergebnisse. Man kann die Wechselspannung auch generieren indem man nur die Spannung ein- und ausschaltet, jedoch hat man dann sekundär auch nur die halbe Spannung. Daher ist eine H-Bridge und Richtungsumschaltung wesentlich günstiger.
Das dazu passende Beispielprogramm für einen AVR ATMega 128
'################################################### ' PowerMotorDriverFrequenzgenerator ' für ' Controllerboard Board mit Mega128 für ' die Serie RN-Modular, dem modularen ' AVR Entwicklungssystem ' 'Aufgabe: ' Ansteuerung des Pololu Power Motor Driver 36v9 ' Erzeugt eine Konstante Frequenz am Ausgang OC1A (Kein PWM) 'Autor: Frank 'Infos:http://www.Roboternetz.de oder https://www.mikrocontroller-elektronik.de/ '####################################################### $programmer = 12 'MCS USB (Zeile weglassen wenn anderer Programmer) ' ---------------RN-Mega128 übliche ------------------ $regfile = "m128def.dat" ' Bei Mega 128 " $framesize = 64 $swstack = 64 $hwstack = 64 $crystal = 16000000 'Quarzfrequenz Config Pine.3 = Output Motorboard_richtung Alias Porte.3 Config Pina.1 = Output Motorboard_reset Alias Porta.1 Config Pine.4 = Output Motorboard_pwm Alias Porte.4 Config Timer3 = Timer , Prescale = 1 , Compare A = Toggle , Clear Timer = 1 Motorboard_reset = 1 Motorboard_pwm = 1 Motorboard_richtung = 1 Enable Timer3 Start Timer3 ' Compare3a = 100 '79,2 khz ' Compare3a = 200 '39,7 khz ' Compare3a = 300 '26,5 khz ' Compare3a = 400 '20 khz ' Compare3a = 500 '16 khz Compare3a = 600 '13,3 khz ' Compare3a = 700 '11,4 khz ' Compare3a = 800 '10 khz ' Compare3a = 900 '8,9 khz ' Compare3a = 1000 '8 khz ' Compare3a = 2000 '4 khz ' Compare3a = 3000 '2,6 khz ' Compare3a = 4000 '2 khz ' Compare3a = 10000 '800 Hz ' Compare3a = 30000 '266 Hz ' Compare3a = 50000 '160 Hz ' Compare3a = 65000 '123 Hz Do Loop
Schaltungsbeschreibung der Propellerclock
Unsere Propellerclock verfügt über 50 LED´s, wobei 32 blaue auf der einen Seite und 16 rote auf der anderen Seite angeordnet sind. Eine grüne und gelbe befindet sich im Bereich der Mitte.
Die Hauptaufgabe sollen eigentlich die 32 blauen Leds übernehmen, sie reichen aus um zum Beispiel eine Bildauflösung von ca. 200-220 Pixel x 32 Pixel darzustellen. Sie sind so angeordnet dass vom Mittelpunkt bis zum äußeren Ende der „Rotorplatine“ keine Lücke entsteht. Dies ist wichtig wenn man zum Beispiel eine Uhr mit Zeiger darstellen möchte.
Die anderen Leds können genutzt werden um etwas mehr Farbe in die Grafik zu bringen.
Bestückt werden wahlweise Standard SMD Leds (1206 Bauform) oder etwas hellere Osram LED´s (siehe Bauteileliste). Wichtig ist nur das diese nur 20mA verbrauchen, die Durchlassspannung spielt keine Rolle. Leds mit anderen Strömen sind zwar auch möglich, jedoch müsste man dann für R1,R6,R10 einen anderen Wert nehmen.
Angesteuert werden die Leds von einem hochmodernen LED-Treiber TLC59116. Drei solche Treiberbauteine sind vorhanden, jeder steuert 16 LED`s an. Der LED-Treiber sorgt automatisch dafür das jede LED den korrekten Strom von 20 mA erhält. Angesteuert werden die LED-Treiber ganz bequem über den I2C-Bus. Der I2C-Bus darf dabei sogar maximal mit 1 Mhz Takt betrieben werden, dadurch ist eine sehr schnelle Ansteuerung aller Leds möglich. Jede kann beliebig ein oder ausgeschaltet werden. Eigentlich ist damit der TLC59116 noch unterfordert, denn er kann noch mehr. Er kann auch die Helligkeit jeder einzelnen LED verändern, dazu muss lediglich das Ansteuerprogramm geändert werden. Allerdings wird diese Möglichkeit in unserem ersten Beispielprogramm nicht genutzt. Würde man diese Fähigkeit nutzen so müsste man auch die Bildwiederholungsrate sehr zurücknehmen oder nur wenige Leds zur Anzeige nutzen weil sonst einfach das Timing zu knapp wird, der Controller wird es dann kaum noch schaffen die Leds rechtzeitig zu aktualisieren da ja mit den Helligkeitswerten viel mehr Daten übertragen werden müssen.
Aus diesem Grunde empfehlen die enormen Fähigkeiten des TLC59116 ruhig mal alle zu testen damit man sie vielleicht auch bei anderen Projekten anwenden kann. Jedoch dann bei der Propelleruhr nur den Mode zum Ein- und Ausschalten der Leds zu nutzen. Im Bascom Beispielprogramm, das mit der Platine geliefert wird, sieht man genau wie dies funktioniert. Ein Datenblatt des TLC59116 mit all seinen I2C Befehlen findet ihr am Ende des Beitrages.
Als Hauptcontroller verwendet unsere Propellerclock einen AVR ATMega644. Es könnte aber auch jeder andere kompatible AVR Controller mit gleicher Bauform verwendet werden. Er sollte nur 20 Mhz verkraften, da unser verwendeter Oszillator 20 Mhz Takt liefert. Die Entscheidung für den Mega644 viel wegen des Taktes und den 4kByte Ram sowie 65KB Flash über die er verfügt. So haben wir genügend Speicher um sogar kleine Animationen einzuprogrammieren.
Datenübertragung vorgesehen
Ich habe auch noch einen zweiten Co-Controller (Mega168 20 Mhz) vorgesehen. Dieser muss nicht unbedingt bestückt werden. Er ist nur dann sinnvoll wenn Daten während des Rotierens auf die Propellerplatine übertragen werden sollen, zum Beispiel Texte, Uhrzeit oder Bilder die angezeigt werden sollen. Für diesen Zweck führt eine Halbwelle der Wechselspannung auf PD2 (INT0) und PB0 (ICP1). Also auf einen Interrupt Eingang und einen Timer Capture Eingang. Dadurch kann der CoController jederzeit genau messen wie lange eine Halbwelle dauert (woraus er die Frequenz errechnen kann).
Wenn nun die Frequenz der Wechselspannung der Primärspannung leicht geändert wird, erkennt dies somit der Co-Controller. Dies kann genutzt werden indem man die Frequenz im binären Rhythmus ändert, also bei 1 eine andere Frequenz als bei 0. Somit könnte der CoController Binärzahlen decodieren , also Daten empfangen. Synchronisieren müsste man das ganze dann noch, am einfachsten mittels Umdrehung. Immer wenn eine Umdrehung rum ist, wird eine 1 oder 0 übertragen.
Wan eine Umdrehung rum ist, wird durch einen Hallsensor ermittelt. Der Hallsensor reagiert auf einen Magneten an dem er bei jeder Runde vorbeikommt.
Aber auch der Controller der die Wechselspannung generiert muss erkennen wann eine Runde vorbei ist. Dazu kann eine IR-LED (D7) zu Hilfe genommen werden. Sie kann ein Lichtsignal senden das z.B. von einem Fototransistor empfangen wird. Alternativ kann natürlich auch eine Reflexlichtschranke einfach das Rotorblatt erfassen, das kann jeder nach Belieben umsetzen.
Die Daten die der Co-Controller empfängt, könnte er dann per RS232 zum Hauptcontroller senden. Achtung, hier muss beim Co-Controller der RX-Pin zum senden verwendet werden, man muss also die Software RS232 von Bascom zum Senden nutzen. Dies liegt daran das RX und TX beider Controller parallel geschaltet auf einen 4 poligen Stecker führen. An diesem Stecker kann man während der Programmierung ein (über Pegelwandler Max232) PC mit Terminalprogramm anschließen um mit den Controllern zu kommunizieren. Zum Beispiel um Variableninhalte zu debuggen. Achtung, nie bei beiden Controllern gleichzeitig den Hardware Uart (RS232) nutzen.
Leider bin ich nicht mehr dazu gekommen um auch ein Beispielprogramm für die Datenübertragung zu schreiben, zumal ich es selbst für meine Anwendung nicht brauche. Aber vielleicht habe ich später noch Lust und Zeit dazu oder aber ein anderer Bastler stellt ein passendes als Kommentar hier rein.
Erwähnen möchte ich noch dass selbst ohne CoController die Datenübertragung möglich ist, denn die Halbwelle wird nicht nur auf den CoController sondern auch auf den Capture Eingang PD6(ICP) des Hauptcontrollers geleitet. Allerdings hat der Hauptcontroller mit der Anzeige soviel zu tun, das er Daten vermutlich nur dann empfangen kann wenn er die Leds nicht gleichzeitig noch aktualisieren muss!
Erwähnenswert sind noch die zwei Fototransistoren auf der Platine. Eine befindet sich auf der Forderseite und eine auf der Rückseite. Sie führen zu einem analogen Eingang. Sie können wahlweise beide oder auch nur einer von ihnen bestückt werden. Sie können verschiedene Aufgaben erfüllen, zum Beispiel einfach um die Zimmerhelligkeit zu messen und die LED Helligkeit anzupassen. Denkbar wäre aber auch das nur der auf der Rückseite bestückt wird. Er könnte dann Rückmeldungen einer IR-Led registrieren. Denkbar wäre so eventuell auch eine Datenübertragung über diesen Fototransistor, ganz ohne Spulenfrequenzen. Auch dieser Empfang könnte mit der Umrundung synchronisiert werden. Aber das ist nur so ein Gedanke, ich habe es nicht ausprobiert, aber halt mal für Leute vorgesehen die gerne an solchen Timing-Software-Dingen basteln.
Zur Programmierung ist noch zu sagen das für den Hauptcontroller und den CoController jeweils eine 10 poliger ISP-Buchse auf der Platine vorhanden ist. Die Belegung entspricht dem üblichen ISP-Standard sowie es in den RN-Definitionen beschrieben ist. Allerdings wurde eine kleinere Buchse verwendet, da die großen Wannenbuchsen einfach weniger gut für die rotierende Platine geeignet waren. Dennoch können die üblichen 10 poligen Programmieradapter wie (ISP, Bascom USB-ISP usw.) zur Programmierung verwendet werden. Es muss lediglich noch ein zusätzlicher kleiner roter Stecker (Reichelt Best.Nr. MM SL 10SK) an das übliche ISP Kabel angepresst werden (siehe Foto).
So das waren eigentlich die wichtigsten Dinge die zur Schaltung zu sagen sind. Die anderen Eigenschaften und Merkmale könnt ihr aus dem Schalt- und Bestückungsplan entnehmen. Ihr findet dort auch eine Beschreibung aller verwendeten Bauteile und deren Bezugsquelle.
Somit steht einem Bau einer Propellerclock nix mehr im Wege. Mit etwas Elektronik Grundkenntnissen und SMD Löterfahrung sollte das ganze nicht weiter schlimm sein. Aber etwas SMD Löterfahrung sollte schon vorhanden sein. Mit genügend Flußmittel lassen sich die kleinen Bauteile übrigens besser löten als man herkömmlich denkt.
Viel Spaß und gutes Gelingen!
Schaltplan
Bestückungsplan (Top-Seite)
Bauteileliste und Bezugsquellen
Menge Wert Bauteile Anmerkung / Bezugsquelle ---------------------------------------------------------------------------------------------- 32 LED1 bis LED32 Blaue LED`s möglichst hell Entweder normale LED`s (1206 Bauform) oder OSRAM TOPLED, Bezugsquelle* Reichelt 16 LED33 bis LED48 Orange LED`s möglichst hell Entweder normale LED`s (1206 Bauform) oder OSRAM TOPLED, 355 mcd, orange Bezugsquelle* Reichelt (beide passen) 1 LED49 Gelbe LED möglichst hell Entweder normale LED`s (1206 Bauform) oder OSRAM TOPLED, 355 mcd,gelb Reichelt Bezugsquelle* Reichelt (beide passen) 1 LED50 Rote LED möglichst hell Entweder normale LED`s (1206 Bauform) oder OSRAM TOPLED, 224 mcd, superrot Reichelt.de Artikel-Nr.: LS T67B Bezugsquelle* Reichelt 1 OSZILLATOR_AQO7050 OSZILLATOR 20 Mhz Buerklin Elektronik Nr.77 D 6934 1 4,7V zehnerdiode ZENER-DIODE SOT23 D6 Bezugsquelle* Reichelt 7 10k R3, R4, R7, R8, R9, R14, R15 Bezugsquelle* Reichelt 1 20k R11 Bezugsquelle* Reichelt 1 22k R5 Bezugsquelle* Reichelt 1 100k R13 Bezugsquelle* Reichelt 10 100n C1, C4, C7, C8, C9, C10, C11, C12, C14, C15 Bezugsquelle* Reichelt 1 100uF/6,3V C5 Bezugsquelle* Reichelt 3 200 R12, R16, R17 Bezugsquelle* Reichelt 1 470uF/25V C2 Bezugsquelle* Reichelt 3 910 Ohm R1, R6, R10 Bezugsquelle+ Reichelt 1 1500uF/6,3V C3 Bezugsquelle* Reichelt 1 IR Led SFH420 SFH420_IRLED D7 Bezugsquelle* Conrad 5 MBRS240 MBRS240 D1, D2, D3, D4, D5 Bezugsquelle* Reichelt 1 MEGA48/88/168-AU MEGA168-AU IC8 Bezugsquelle* Reichelt 1 MEGA644 MEGA644 20Mhz IC6 Bezugsquelle* Reichelt 1 MICROMATCH-4 MICROMATCH-4 RS232 Micromatch Federleiste gerade 4p Bezugsquelle* Reichelt 2 MICROMATCH-10 MICROMATCH-10 ISP1, ISP2 Micromatch Federleiste gerade 10p Bezugsquelle* Reichelt 1 SFH320 SFH320 T2 Bezugsquelle* Reichelt 2 SMD TAN.100/6,3 C6, C13 Tantal 100uF Reichelt Bezugsquelle* Reichelt 3 TLC59116 TLC59116 IC1, IC2, IC3 Bezugsquelle Farnell 1 TLE4905 TLE4905 SOT89 IC7 Ebay* oder Buerklin 1 VARISTOR VARISTOR R18 Bezugsquelle* Reichelt 1 mc7805 MC7805BDTG IC5 SMD 5V/1A Spannungsregler Bezugsquelle Farnell Unbestückt lassen: POWER - Hier kann wahlweise auch eine zweipolige Stiftleiste angelötet werden. Über Power wird das Board mit Spannung versorgt (Gleich- oder Wechselspannung 7 – 15V) C16 Vorgesehen für Goldcap – falls man Board über Schleifer versorgt R2 Vorwiderstand für das optionale Goldcap T1 Der Fototransistor ist nur notwendig wenn die Raumhelligkeit gemessen werden soll Dies kann unter Umständen jedoch auch über T2 auf der Rückseite erfolgen Angaben ohne Gewähr!
Video
Downloads
Datenblatt TLC59116 (PDF)
Eagle-Platinenlayout (ZIP)
Bascom Beispielprogramm
Leiterplatte zum Projekt bestellen
Neu! Die Leiterplatte für dieses Projekt ist direkt über den Shop PlatinenCenter erhältlich. Da die Platinen dort vorgefertigt werden, sind diese sehr preiswert lieferbar.
Individuelle Leiterplatten
Möchtest du keine vorgefertigte Leiterplatte, weil Du vielleicht vorher Änderungen an dem Layout vornehmen möchtest, dann empfehlen ich die Anbieter auf unserer Leiterplatten-Service Seite.
Das Leiterplattenangebot ist ein Service Angebot der jeweiligen Anbieter. Bei Fragen bezüglich Lieferung und Preis bitte dort nachfragen!
Links zum Thema
Geeignete Programmer für die Programmierung
Letzte Aktualisierung am 1.04.2025 / * Affiliate Links
Weitere Hinweise
Vor dem Aufbau bitte nachfolgende Hinweise lesen:Das Projekt unterliegt einer CC-Lizenz - Lizenzhinweis (zum Aufklappen anklicken)
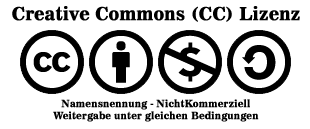
Falls Dir der Beitrag gefallen oder geholfen hat kannst Du dem Autor aber gerne durch eine kleine Spende Danke sagen!